Home / FAQ / TECHNICAL ARTICLES / HIGH TEMPERATURE CHALLENGES AND SOLUTIONS FOR POWER SUPPLIES
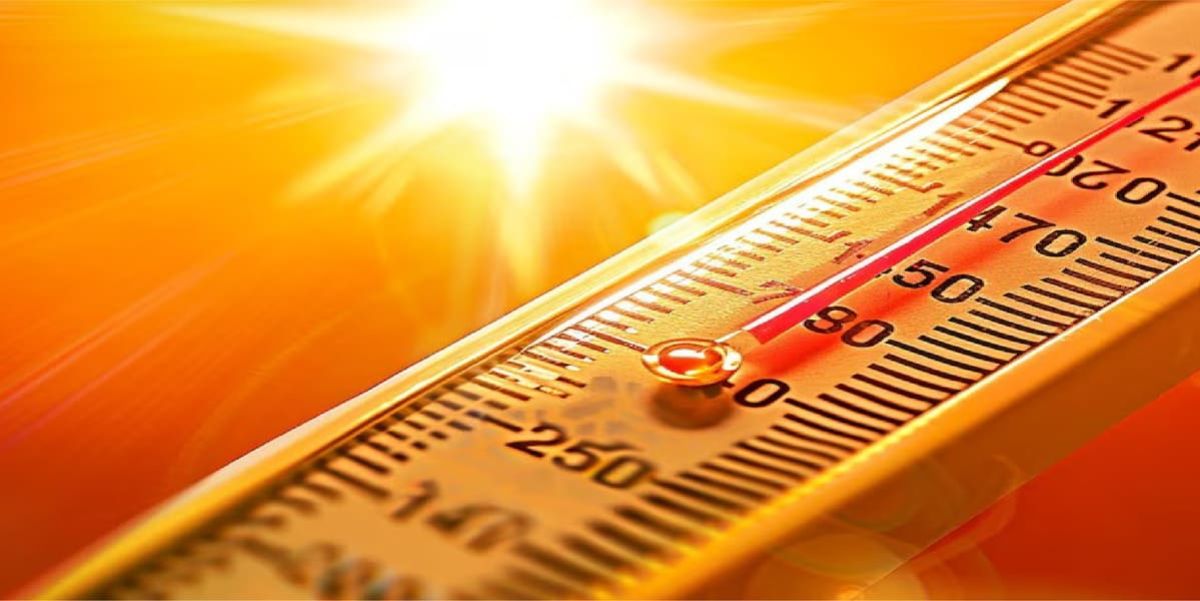
High Temperature Challenges and Solutions for Power Supplies
Temperature plays a pivotal role in the design and operation of power supplies, significantly influencing their performance, lifespan, and safety. Both external environmental temperatures and internal heat generated during operation can directly affect a power supply’s stability and efficiency. Without effective thermal management, especially under high loads or extreme conditions, power supplies may experience performance degradation, component damage, or severe issues such as overheating and fire hazards.
This article delves into the mechanisms by which temperature impacts power supplies, examining the dual effects of environmental and internal heat on product performance. It also explores strategies for selecting the right power supply, focusing on the use of derating curves and wide-temperature-range designs. Additionally, we discuss common cooling methods, including natural convection and fan-forced cooling, to help users achieve optimal thermal control across various application scenarios.
By providing a comprehensive understanding of the relationship between temperature and power supplies, this article aims to equip users with effective thermal management strategies, ensuring long-term stable and reliable system operation.
1. The Effects of Temperature on Power Supplies
Rising ambient temperatures can significantly impact the performance of power supplies, reducing the stability of internal electronic components, shortening their lifespan, and causing operational instability in the system. This is particularly pronounced in enclosed devices, where the power supply generates heat during operation due to energy losses, and additional heat from other components, such as the motherboard, further elevates the internal temperature. When external temperatures are high, cooling efficiency decreases, making it harder to dissipate heat effectively. This leads to a continuous rise in internal temperature, creating a vicious cycle that negatively affects the power supply’s performance on multiple levels.
The consequences of high temperatures are both extensive and severe. They not only reduce the operational efficiency and stability of power supplies, resulting in energy waste, but also alter material properties—such as causing expansion or electrolyte leakage—damage components, and decrease reliability, ultimately shortening the product’s lifespan. Excessive internal temperatures can also lead to insulation failure or mechanical loosening, further compromising the power supply’s performance. These issues not only jeopardize the stable operation of equipment but also pose significant safety risks, such as overheating or fire hazards.
Therefore, effective control of both ambient and internal temperatures is essential for ensuring the reliability and longevity of power supplies.
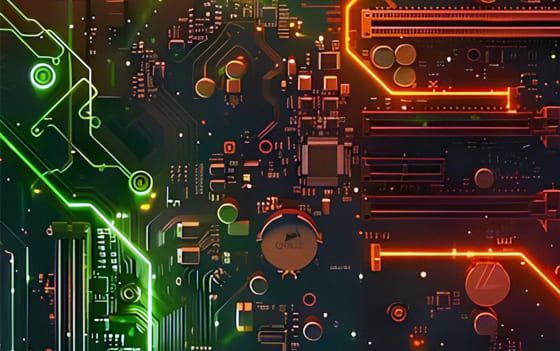
2. Operating Temperature Range of Power Supplies
The operating temperature specified for a power supply refers to the temperature of the environment around it, rather than the external ambient temperature of the equipment. Typically, the operating temperature range for power supplies is between 0°C and 40°C, with some products able to reach standards of 0°C to 50°C. In other words, the temperature inside the equipment must be maintained within this range to ensure stable operation.
However, if the external ambient temperature of the equipment is too high, it can reduce the overall heat dissipation efficiency, causing the internal temperature of the device to rise and affecting the power supply’s performance. Additionally, due to inadequate heat dissipation from other components or poor ventilation, the actual internal temperature of the equipment is often higher than the external environment temperature. Therefore, when selecting and using a power supply, careful consideration must be given to whether the actual operating temperature inside the equipment falls within its specified operating temperature range. Furthermore, proper cooling measures should be implemented to prevent the temperature from exceeding the limits, which could impact performance or cause damage to the equipment.
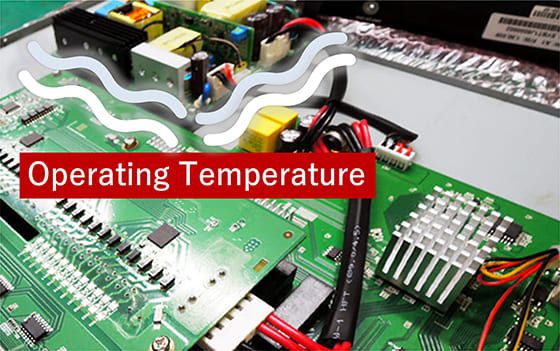
The operating temperature refers to the ambient temperature surrounding the power supply.
3. Wide Temperature Power Supplies and Derating Curve
The operating temperature range for standard power supplies typically falls between 0°C and 40–50°C. When the ambient temperature exceeds this range—such as during scorching summers or freezing winters—the power supply may fail to operate normally. To address such extreme environments, users are advised to opt for wide temperature (Wide Temperature) power supplies. These devices are designed to provide stable power even under high or low-temperature conditions, ensuring the reliable operation of connected equipment. Wide temperature power supplies usually operate within a range of -40 to -20°C up to 70–80°C, exceeding the range of conventional power supplies and meeting the needs of most applications.
Although wide temperature power supplies utilize internal components with superior heat resistance, these materials still have thermal and efficiency limits. When the ambient temperature exceeds 40–50°C (depending on the product design), internal components may overheat, leading to performance degradation and reduced output power. As the ambient temperature rises, the power supply’s load capacity gradually decreases, resulting in a corresponding reduction in output power. This phenomenon can be represented by a derating curve, which users should consult to adjust load power accordingly. In high-temperature environments, it is particularly important to reduce the load appropriately to prevent overloading the power supply, thereby ensuring system stability.
For example, Tiger Power’s latest 750W TN24-0750 series power supply operates within a temperature range of -40°C to 70°C. Within -40°C to 50°C, the power supply can reliably deliver 700W of power. However, as the temperature rises to 50–70°C, the output power decreases gradually, dropping to 400W at 70°C. If the ambient temperature exceeds 70°C, the over-temperature protection function activates, halting output until the temperature returns to a safe range.
Therefore, if the working environment temperature ranges between 50°C and 70°C and the load requirement is between 400W and 700W, customers are advised to select a higher wattage wide temperature power supply and strictly follow the derating curve guidelines. This approach not only ensures stable operation under high temperatures but also effectively safeguards the performance and safety of the equipment.
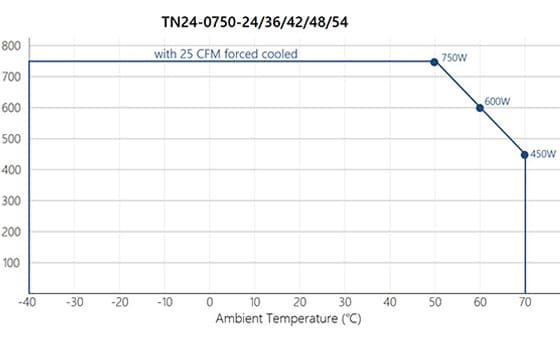
The Derating Curve of Power Supplies
4. Heat Dissipation and Cooling Methods for Power Supplies
Power supplies generate heat during operation, with the amount increasing in proportion to the output power. To ensure stable operation, this heat must be effectively dissipated. Common designs typically incorporate aluminum extruded heat sinks to enhance thermal performance and employ either fan-forced cooling or natural air convection cooling based on airflow requirements.
(1) Fan-Forced Cooling
Fan-forced cooling uses airflow generated by fans to quickly remove heat, making it an effective solution for high-power or high-density systems.
A. Advantages:
Efficient Heat Dissipation: Ideal for prolonged high-power operations, significantly enhancing cooling performance.
Stable Operation: Maintains the reliability and stability of power supplies under high thermal loads.
Intelligent Noise Reduction: Tiger Power’s power supplies can adjust fan speeds based on actual loads, reducing noise and extending fan lifespan.
B. Disadvantages:
Noise Impact: Fan operation generates noise, which may not be suitable for noise-sensitive environments.
Increased Power Consumption: Fans consume additional power and require installation, slightly raising operating costs.
Maintenance Requirements: Fans are consumable components with limited lifespans, necessitating periodic inspection and replacement.
(2) Natural Air Convection Cooling
Natural cooling relies on ambient airflow for heat dissipation, eliminating the need for fans. It is suited for low-power devices and applications with modest cooling requirements.
A. Advantages
Silent Operation: The absence of fans completely removes noise, making it ideal for quiet environments such as hospitals and laboratories.
High Reliability: With no fan components, maintenance needs and potential failure risks are minimized.
B. Disadvantages
Limited Cooling Efficiency: Ineffective for high-power or high-density systems.
Power Output Constraints: To prevent overheating, the output power may need to be reduced, potentially impacting application performance.
Some power supplies are designed to support both fan-forced and natural cooling modes. Fan-forced cooling facilitates efficient heat removal and supports rated power output, while natural cooling, lacking fan assistance, has reduced heat dissipation capacity and consequently lowers output power.
For instance, Tiger Power’s newly developed 750W – TN24-0750 series power supply delivers a rated output of 750W when used with a 25CFM fan. In contrast, under natural cooling, the output drops to 450W.When selecting a cooling method, it is essential to balance application needs and environmental conditions. Fan-forced cooling is ideal for high-power, high-density applications to ensure stable operation, while natural cooling is better suited for noise-sensitive environments.
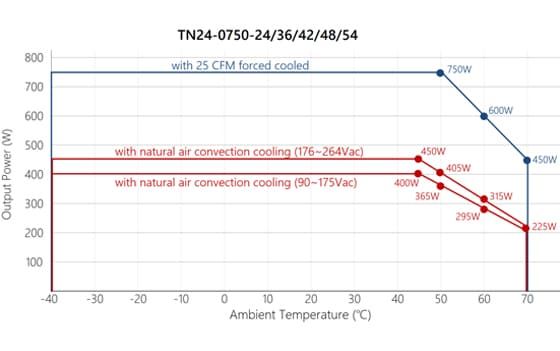
Fan-Forced Cooling vs. Natural Air Convection Cooling
5. Key Considerations When Selecting a Power Supply
Selecting the appropriate power supply is crucial for the stable operation and optimal performance of a system. When choosing, in addition to considering basic specifications such as wattage, voltage, current, and size, it is also necessary to evaluate the installation environment, cooling methods, and other important factors. Below are specific recommendations:
(1) Power and Efficiency
A. Adequate Power Margin
It is recommended to choose a power supply with a 20%-30% power margin based on the system’s total power requirements. This prevents prolonged full-load operation and overuse, enhancing system stability and extending the lifespan of the equipment.
B. Future Scalability
If the system is likely to increase its load in the future, it is advisable to leave space for additional power supplies (e.g., a second or third unit), or choose a model with higher output power. This avoids the risk of overloading and reduces future costs associated with replacing an underpowered supply.
C. Efficiency Standards
Among products with similar specifications, prioritize power supplies with higher efficiency, such as those certified with 80 PLUS Gold or Platinum. High-efficiency products not only reduce energy loss and heat generation but also lower cooling demands, saving energy and reducing operational costs.
(2) Cooling Methods and Layout Design
A. Space Planning and Installation Environment
Ensure the equipment has enough installation space, particularly for cooling requirements. If space is limited or the environment is unsuitable for fan use, opt for power supplies that support natural cooling.
B. Considerations for Natural Cooling
Natural cooling eliminates the need for a fan, but this may result in reduced power output. The device should be equipped with effective ventilation or auxiliary cooling devices (e.g., heat sinks or thermal pads) to ensure effective heat dissipation. This design is especially useful in noise-sensitive or low-maintenance environments.
C. Airflow Direction and Installation
The cooling efficiency of a power supply is affected by ventilation hole design, airflow size, and direction. During installation, ensure that airflow paths are unobstructed and avoid unnecessary or improper ventilation designs that could disrupt airflow. Fans can be installed as needed, and airflow is typically measured in CFM (Cubic Feet per Minute). While larger CFM provides stronger airflow, excessive airflow may have limited impact on cooling and could waste energy. The direction of airflow should be selected based on the system’s requirements, either Air Flow In or Air Flow Out, to achieve optimal cooling. Tiger Power’s intelligent, temperature-controlled fan design adjusts speed based on load conditions, providing the right amount of airflow to prevent overloading and extend the fan’s lifespan.
D. Impact of Placement Orientation
The cooling efficiency of the power supply may vary depending on whether it is mounted horizontally or vertically. It is recommended to choose the installation orientation that provides the best cooling performance based on actual test results.
(3) Environmental and Operating Conditions
A. Operating Temperature and Humidity
Select a power supply that can handle the expected operating environment and temperature range. For high-humidity or dusty environments, consider products designed with waterproof and dustproof features.
B. Vibration and Protection
In specialized applications such as industrial or transportation environments, it is recommended to choose products that are vibration-resistant and shockproof, and ensure the protection level meets the relevant safety standards.
(4) Customization and Technical Support
Tiger Power is dedicated to providing comprehensive customization services. When existing products do not fully meet customer needs, we assist in selecting similar products and conduct in-depth analysis based on real-world applications, offering specific improvement plans. We can perform design modifications, adjust product specifications, and further optimize performance to address challenges in unique application scenarios. In addition, Tiger Power offers full technical support, including assistance with testing and certification to ensure product reliability and compatibility. Through professional customization services, we help customers achieve higher efficiency and optimized system performance.
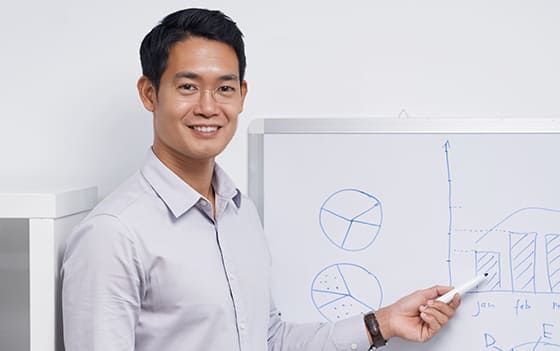